Dust Extraction
Industry Sectors
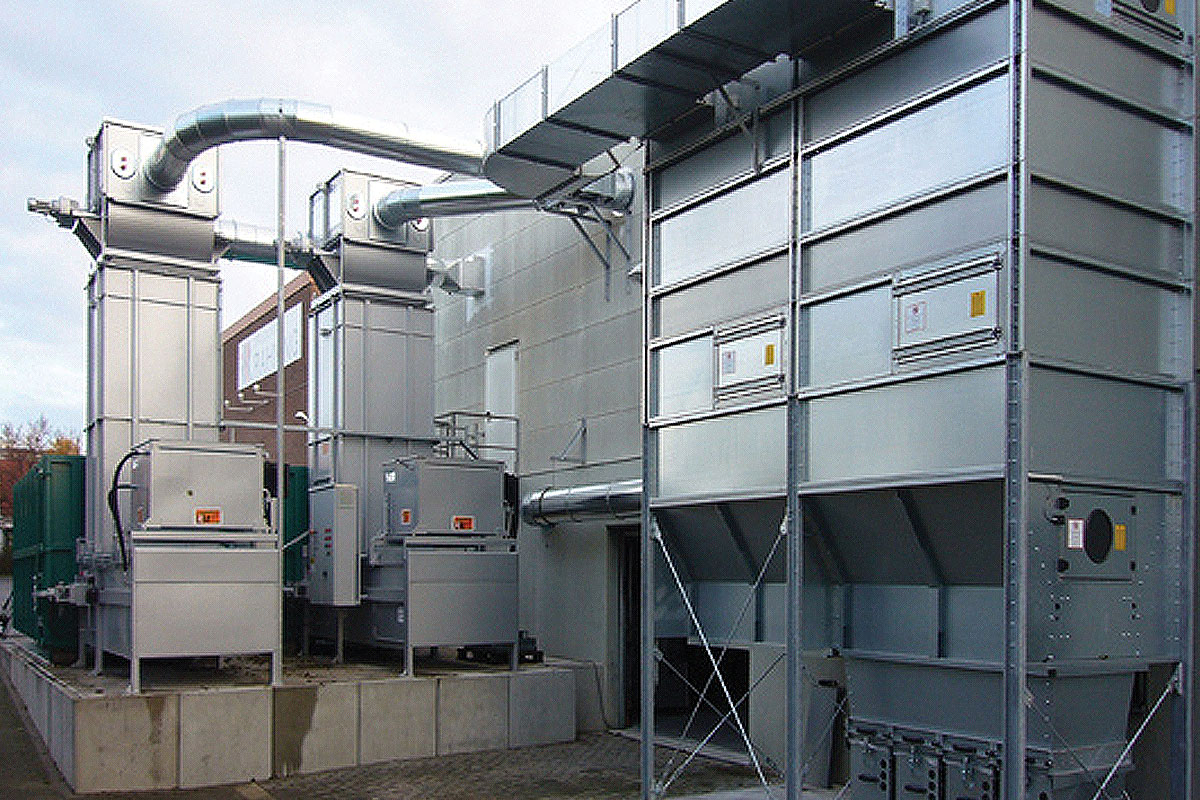
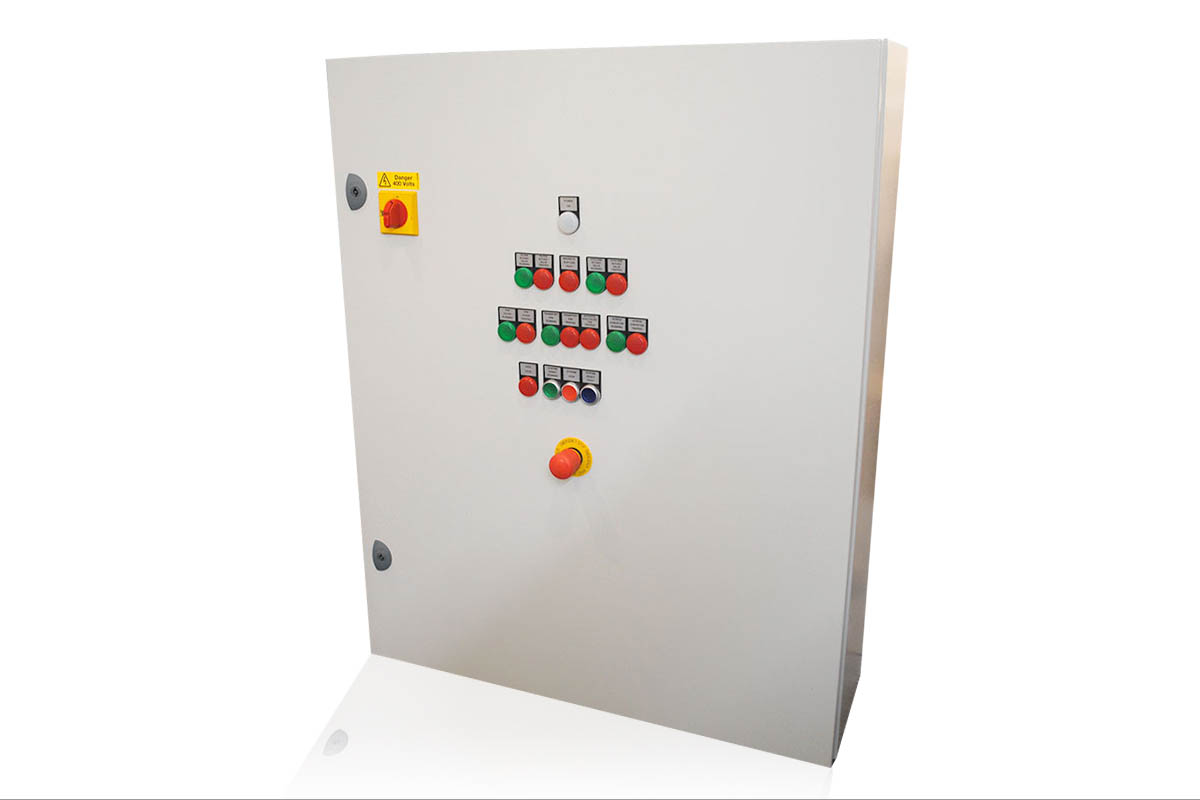
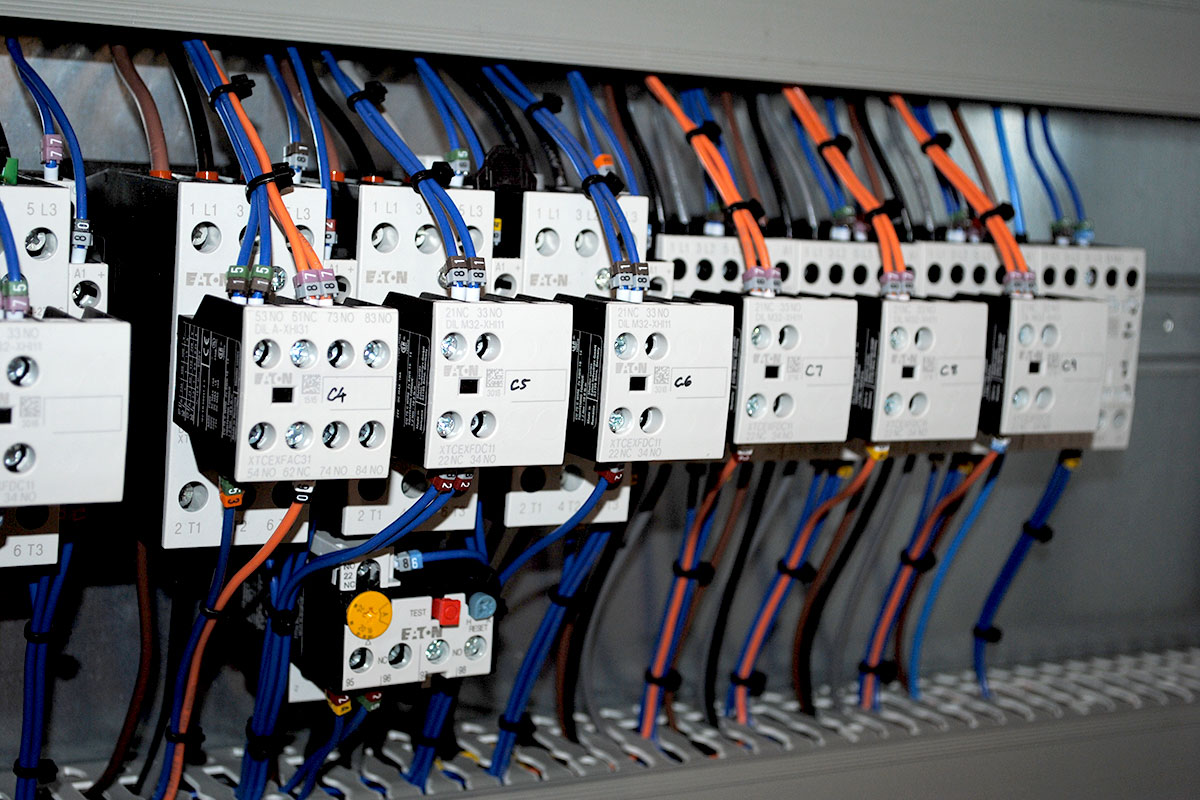
Dust Extraction
RDM Controls specialise in the manufacture of quality control systems for the dust extraction industry, catering for standard products to the complex multi-function wood waste systems.
Quality
Due to the long history in the extraction industry our products are manufactured to meet the demands of the industry. Competitive purchasing enables us to pass on the benefits to our customers without compromising on quality.
Support
We understand the complication and cost implications when a control system breaks down and can offer a wide range of off the shelf D.O.L starters and auto shakers which can be dispatched within 24 hours of receipt of an order. Should your requirements be a non standard control system we are usually able to manufacture replacements within a short period of time due to the large range of stock carried by RDM Controls.
All our customers can benefit from our free telephone technical support in the event of simple enquiries or complex diagnosis when installation or commissioning commences. We also offer onsite technical support at competitive rates, providing peace of mind in the event of any problems.
Inverter Drives
As our energy reserves dwindle while costs continue to rise and as the spectre of climate change looms ever larger, it becomes ever more imperative to take action on energy savings.
Cube Law
Fitting inverter drives to ac motors controlling fans and pumps that run continuously can save considerable amounts of money. This is because the load follows what is termed the cube law, which simply means any reduction in motor speed reduces the power by the same factor, cubed, i.e. the reduction in power absorbed for just a 5% reduction in motor speed is shown by (1-(0.95×0.95×0.95)*100) = 14.3% saving.
Energy costs are set to continue rising for the foreseeable future. Variable speed drives provide the ideal solution to maximising the energy efficiency of electric motors.
Hazardous Areas
Any business that produces potentially explosive gasses, mists, vapours or combustible dusts must now comply with Hazardous Area regulations. The Dangerous Substances and Explosive Atmospheres Regulations (DSEAR) 2002 places the duty to eliminate or control risks from explosion on the employer. DESAR define and explosive atmosphere as a mixture of dangerous substances with air under atmospheric conditions, in the form of gasses, mist or dust in which, after ignition has occurred, combustion spreads to the entire unburned mixture. RDM Controls have been dealing with hazardous areas for many years. As a result of their experience it’s safe to say that every eventuality is considered when designing systems for hazards of this type.
Zone 22
A zone 22 control panel may look like most other control panels but that’s where the similarity stops. The enclosure is tested and certified for impact resistance and rated Ex. and the push buttons are rated for zone 22 Ex. When the panel is finished it is tested at full load current and temperature recorded, only if all falls within BSEN 50281-1:1999 & BSEN 50281-1-2:1999 limits, will the certificate be issued and the certification plate is attached to the control panel enclosure.
Zone 20/21
Zone 20/21 areas are related to dust where an explosive atmosphere is constantly present or is likely to occur in normal operation. The construction of the enclosure has to be so that if there is an ignition within the enclosure it can’t escape therefore preventing the explosion. These panels are highly specialised and cannot be changed once documented and certified.
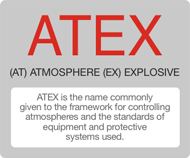

We’ve built Electrical Control Panels for:
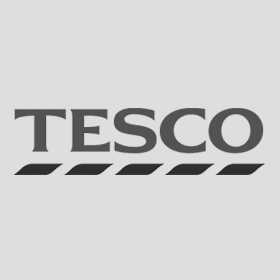



